Modelling and Simulation
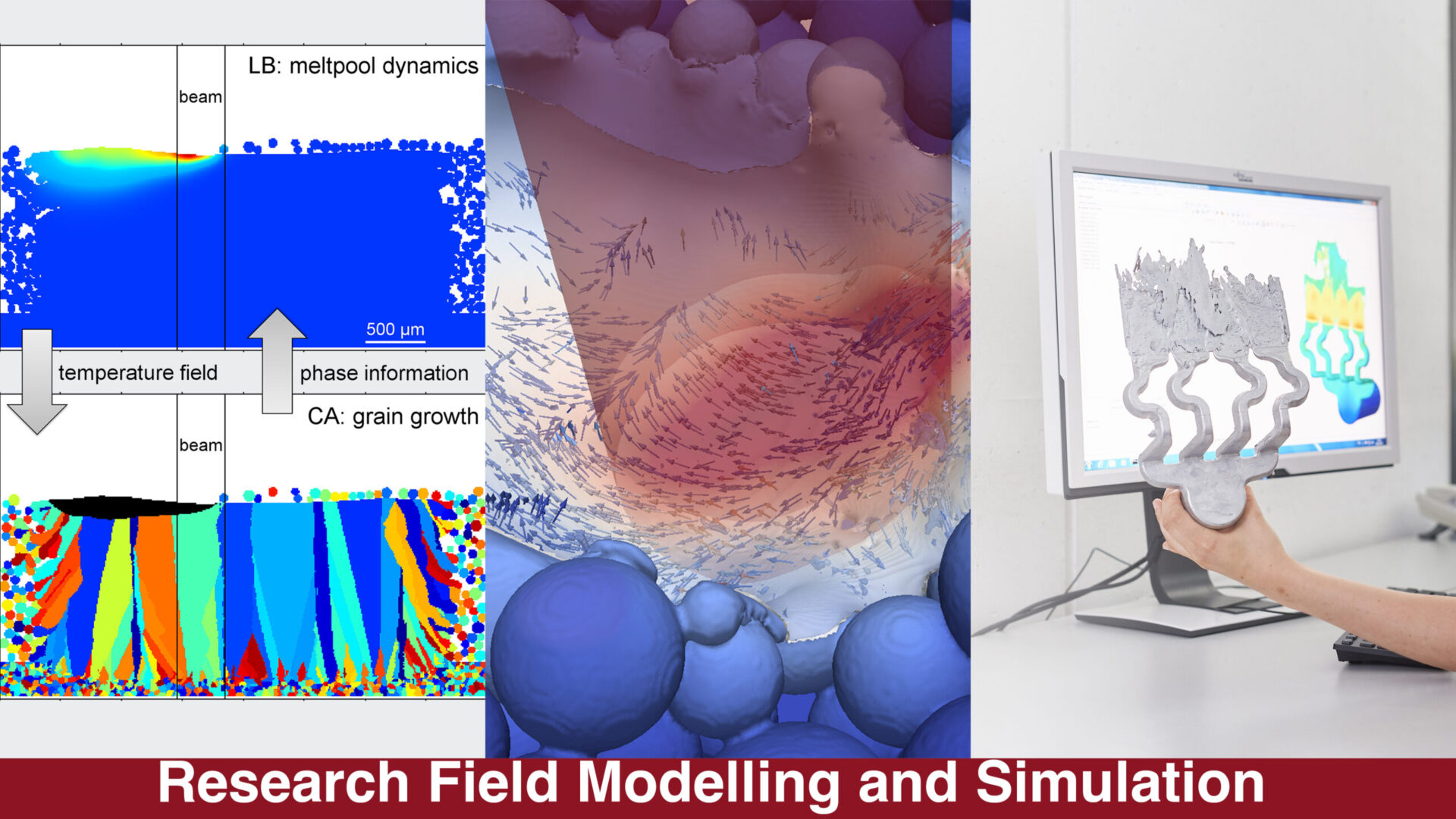
The group Modelling and Simulation develops and implements new software:
- Process simulation of beam-based additive manufacturing in powder beds
- Multi-criteria optimization for alloy development
- Process simulation of foam formation
Journal Articles
Effect of scanning strategies on grain structure and texture of additively manufactured lattice struts: A numerical exploration
In: Advanced Engineering Materials (2024)
ISSN: 1438-1656
DOI: 10.1002/adem.202400661 , , , :
Graph-based spot melting sequence for electron beam powder bed fusion
In: Additive Manufacturing 91 (2024), Article No.: 104321
ISSN: 2214-7810
DOI: 10.1016/j.addma.2024.104321 , , :
Extracting powder bed features via electron optical images during electron beam powder bed fusion
In: Additive Manufacturing Letters 10 (2024), Article No.: 100220
ISSN: 2772-3690
DOI: 10.1016/j.addlet.2024.100220 , , , , :
Multiple interaction electron beam powder bed fusion for controlling melt pool dynamics and improving surface quality
In: Additive Manufacturing 90 (2024), Article No.: 104316
ISSN: 2214-7810
DOI: 10.1016/j.addma.2024.104316 , , :
A new approach of preheating and powder sintering in electron beam powder bed fusion
In: International Journal of Advanced Manufacturing Technology (2024)
ISSN: 0268-3768
DOI: 10.1007/s00170-024-13966-1 , , , :
A CALPHAD-Informed Enthalpy Method for Multicomponent Alloy Systems with Phase Transitions
In: Modelling 5 (2024), p. 367-391
ISSN: 2673-3951
DOI: 10.3390/modelling5010020 , , , :
Comprehensive numerical investigation of laser powder bed fusion process conditions for bulk metallic glasses
In: Additive Manufacturing 81 (2024), Article No.: 104026
ISSN: 2214-7810
DOI: 10.1016/j.addma.2024.104026 , , :
Numerical Microstructure Prediction for Lattice Structures Manufactured by Electron Beam Powder Bed Fusion
In: Crystals 14 (2024), Article No.: 149
ISSN: 2073-4352
DOI: 10.3390/cryst14020149 , , , :
Design and Characterization of a Novel NiAl–(Cr,Mo) Eutectic Alloy
In: Advanced Engineering Materials (2024)
ISSN: 1438-1656
DOI: 10.1002/adem.202302079 , , , , , , :
A Scan Strategy Based Compensation of Cumulative Heating Effects in Electron Beam Powder Bed Fusion
In: Progress in Additive Manufacturing (2024)
ISSN: 2363-9512
DOI: 10.1007/s40964-024-00807-6 , , :
Correction to: A Scan Strategy Based Compensation of Cumulative Heating Effects in Electron Beam Powder Bed Fusion (Progress in Additive Manufacturing, (2024), 10.1007/s40964-024-00807-6)
In: Progress in Additive Manufacturing (2024)
ISSN: 2363-9512
DOI: 10.1007/s40964-024-00841-4 , , :
A thermo-mechanical model for hot cracking susceptibility in electron beam powder bed fusion of Ni-base superalloys
In: Materials & Design 237 (2024), Article No.: 112528
ISSN: 0264-1275
DOI: 10.1016/j.matdes.2023.112528 , , :
Progress in electron beam additive manufacturing
In: Progress in Additive Manufacturing (2024)
ISSN: 2363-9512
DOI: 10.1007/s40964-024-00679-w , , :
Experimental Validation of Property Models and Databases for Computational Superalloy Design
In: Advanced Engineering Materials (2024)
ISSN: 1438-1656
DOI: 10.1002/adem.202401051 , , , , , , , :
A Thermo-Mechanical Model for Hot Cracking Susceptibility in Electron Beam Powder Bed Fusion of Ni-Base Superalloys
In: Materials & Design 237 (2023), p. 112528
ISSN: 0264-1275
DOI: 10.1016/j.matdes.2023.112528 , , :
Volume of fluid based modeling of thermocapillary flow applied to a free surface lattice Boltzmann method
In: Journal of Computational Physics 492 (2023), Article No.: 112441
ISSN: 0021-9991
DOI: 10.1016/j.jcp.2023.112441 , , :
A return time compensation scheme for complex geometries in electron beam powder bed fusion
In: Additive Manufacturing 76 (2023), p. 103767
ISSN: 2214-7810
DOI: 10.1016/j.addma.2023.103767 , , :
Revealing bulk metallic glass crystallization kinetics during laser powder bed fusion by a combination of experimental and numerical methods
In: Journal of Non-Crystalline Solids 619 (2023), Article No.: 122532
ISSN: 0022-3093
DOI: 10.1016/j.jnoncrysol.2023.122532 , , , , , , :
High-Throughput Numerical Investigation of Process Parameter-Melt Pool Relationships in Electron Beam Powder Bed Fusion
In: Modelling 4 (2023), p. 336-350
ISSN: 2673-3951
DOI: 10.3390/modelling4030019 , , , :
Alternative Approach to Modeling of Nucleation and Remelting in Powder Bed Fusion Additive Manufacturing
In: Advanced Engineering Materials (2023)
ISSN: 1438-1656
DOI: 10.1002/adem.202201682 , , , , :
A Ray Tracing Model for Electron Optical Imaging in Electron Beam Powder Bed Fusion
In: Journal of Manufacturing and Materials Processing 7 (2023), Article No.: 87
ISSN: 2504-4494
DOI: 10.3390/jmmp7030087 , , , :
Evaluation of Additively-Manufactured Internal Geometrical Features Using X-ray-Computed Tomography
In: Journal of Manufacturing and Materials Processing (2023)
ISSN: 2504-4494
DOI: 10.3390/jmmp7030095 , , , , , , , , , :
Geometrical Influence on Material Properties for Ti6Al4V Parts in Powder Bed Fusion
In: Journal of Manufacturing and Materials Processing 7 (2023), p. 82
ISSN: 2504-4494
DOI: 10.3390/jmmp7030082 , , , , , , , , , , :
Additive manufacturing of cellular structures: Multiscale simulation and optimization
In: Journal of Manufacturing Processes 95 (2023), p. 275-290
ISSN: 1526-6125
DOI: 10.1016/j.jmapro.2023.03.071 , , , , , , , , , , :
Phase-Field Study of the History-Effect of Remelted Microstructures on Nucleation During Additive Manufacturing of Ni-Based Superalloys
In: Metallurgical and Materials Transactions A-Physical Metallurgy and Materials Science (2023)
ISSN: 1073-5623
DOI: 10.1007/s11661-023-07004-0 , , , , :
Surface topographies from electron optical images in electron beam powder bed fusion for process monitoring and control
In: Additive Manufacturing 60 (2022), Article No.: 103172
ISSN: 2214-7810
DOI: 10.1016/j.addma.2022.103172 , , , :
Numerical Design of CoNi-Base Superalloys With Improved Casting Structure
In: Metallurgical and Materials Transactions A-Physical Metallurgy and Materials Science (2022)
ISSN: 1073-5623
DOI: 10.1007/s11661-022-06870-4 , , , , , , , , , :
Predictive simulation of bulk metallic glass crystallization during laser powder bed fusion
In: Additive Manufacturing 59 (2022), Article No.: 103121
ISSN: 2214-7810
DOI: 10.1016/j.addma.2022.103121 , , :
Basic Mechanism of Surface Topography Evolution in Electron Beam Based Additive Manufacturing
In: Materials 15 (2022), Article No.: 4754
ISSN: 1996-1944
DOI: 10.3390/ma15144754 , , , :
Evolution of an industrial-grade Zr-based bulk metallic glass during multiple laser beam melting
In: Journal of Non-Crystalline Solids 589 (2022), Article No.: 121649
ISSN: 0022-3093
DOI: 10.1016/j.jnoncrysol.2022.121649 , , , , , , , :
How electron beam melting tailors the Al-sensitive microstructure and mechanical response of a novel process-adapted γ-TiAl based alloy
In: Materials & Design 212 (2021), Article No.: 110187
ISSN: 0264-1275
DOI: 10.1016/j.matdes.2021.110187 , , , , , , , , :
A multivariate meltpool stability criterion for fabrication of complex geometries in electron beam powder bed fusion
In: Additive Manufacturing 45 (2021), Article No.: 102051
ISSN: 2214-7810
DOI: 10.1016/j.addma.2021.102051 , , , :
New grain formation mechanisms during powder bed fusion
In: Materials 14 (2021), Article No.: 3324
ISSN: 1996-1944
DOI: 10.3390/ma14123324 , , , , :
A Novel Approach to Predict the Process-Induced Mechanical Behavior of Additively Manufactured Materials
In: Journal of Materials Engineering and Performance (2021)
ISSN: 1059-9495
DOI: 10.1007/s11665-021-05725-0 , , , , , :
Isothermal crystallization kinetics of an industrial-grade Zr-based bulk metallic glass
In: Journal of Non-Crystalline Solids 573 (2021), Article No.: 121145
ISSN: 0022-3093
DOI: 10.1016/j.jnoncrysol.2021.121145 , , , , , :
Modeling laser beam absorption of metal alloys at high temperatures for selective laser melting
In: Advanced Engineering Materials 23 (2021), Article No.: 2100137
ISSN: 1438-1656
DOI: 10.1002/adem.202100137 , , , :
Multi-material model for the simulation of powder bed fusion additive manufacturing
In: Computational Materials Science 194 (2021)
ISSN: 0927-0256
DOI: 10.1016/j.commatsci.2021.110415 , , , :
A versatile cryo-transfer system, connecting cryogenic focused ion beam sample preparation to atom probe microscopy
In: PLoS ONE 16 (2021), Article No.: e0245555
ISSN: 1932-6203
DOI: 10.1371/journal.pone.0245555 , , , , :
Numerical Alloy Development for Additive Manufacturing towards Reduced Cracking Susceptibility
In: Crystals 11 (2021)
ISSN: 2073-4352
DOI: 10.3390/cryst11080902 , , , :
New grain formation by constitutional undercooling due to remelting of segregated microstructures during powder bed fusion
In: Materials 13 (2020), p. 1-14
ISSN: 1996-1944
DOI: 10.3390/ma13235517 , , , , :
Modeling and Simulation of Microstructure Evolution for Additive Manufacturing of Metals: A Critical Review
In: Metallurgical and Materials Transactions A-Physical Metallurgy and Materials Science (2020)
ISSN: 1073-5623
DOI: 10.1007/s11661-020-05946-3 , , :
MultOpt++: a fast regression-based model for the constraint violation fraction due to composition uncertainties
In: Modelling and Simulation in Materials Science and Engineering 27 (2019)
ISSN: 0965-0393
DOI: 10.1088/1361-651X/aaf01e , , , , , , :
MultOpt++: a fast regression-based model for the development of compositions with high robustness against scatter of element concentrations
In: Modelling and Simulation in Materials Science and Engineering 27 (2019)
ISSN: 0965-0393
DOI: 10.1088/1361-651X/aaf0b8 , , , , , , , :
Numerical microstructure prediction by a coupled finite element cellular automaton model for selective electron beam melting
In: Computational Materials Science 162 (2019), p. 148-155
ISSN: 0927-0256
DOI: 10.1016/j.commatsci.2019.03.004 , , , , , :
SAMPLE: A Software Suite to Predict Consolidation and Microstructure for Powder Bed Fusion Additive Manufacturing
In: Advanced Engineering Materials (2019), Article No.: 1901270
ISSN: 1438-1656
DOI: 10.1002/adem.201901270 , , , :
Development of Single-Crystal Ni-Base Superalloys Based on Multi-criteria Numerical Optimization and Efficient Use of Refractory Elements
In: Metallurgical and Materials Transactions A-Physical Metallurgy and Materials Science 49A (2018), p. 4134-4145
ISSN: 1073-5623
DOI: 10.1007/s11661-018-4759-0 , , , , , , , , , , , , , , , , :
Modeling of Laser Beam Absorption in a Polymer Powder Bed
In: Polymers 10 (2018)
ISSN: 2073-4360
DOI: 10.3390/polym10070784 , , , , , :
Powder layer deposition algorithm for additive manufacturing simulations
In: Powder Technology 330 (2018), p. 125-136
ISSN: 0032-5910
DOI: 10.1016/j.powtec.2018.02.026 , :
Predictive simulation of process windows for powder bed fusion additive manufacturing: Influence of the powder size distribution
In: Computers & Mathematics with Applications (2018)
ISSN: 0898-1221
DOI: 10.1016/j.camwa.2018.06.029 , , :
Comparison of passive scalar transport models coupled with the Lattice Boltzmann method
In: Computers & Mathematics with Applications (2018)
ISSN: 0898-1221
DOI: 10.1016/j.camwa.2018.01.017 , , , :
3D multi-layer grain structure simulation of powder bed fusion additive manufacturing
In: Acta Materialia 152 (2018), p. 119-126
ISSN: 1359-6454
DOI: 10.1016/j.actamat.2018.04.030 , , , :
Predictive Simulation of Process Windows for Powder Bed Fusion Additive Manufacturing: Influence of the Powder Bulk Density
In: Materials 10 (2017)
ISSN: 1996-1944
DOI: 10.3390/ma10101117 , , , , :
Macroscopic simulation and experimental measurement of melt pool characteristics in selective electron beam melting of Ti-6Al-4V
In: International Journal of Advanced Manufacturing Technology (2017)
ISSN: 0268-3768
DOI: 10.1007/s00170-016-8819-6
URL: http://link.springer.com/article/10.1007/s00170-016-8819-6 , , , , , :
Simulation of grain structure evolution during powder bed based additive manufacturing
In: Additive Manufacturing 13 (2017), p. 124-134
ISSN: 2214-7810
DOI: 10.1016/j.addma.2016.10.007 , , :
Numerical simulation of multi-component evaporation during selective electron beam melting of TiAl
In: Journal of Materials Processing Technology 247 (2017), p. 280-288
ISSN: 0924-0136
DOI: 10.1016/j.jmatprotec.2017.04.016 , , , :
Additive manufacturing using selective electron beam melting
In: Welding and Cutting (2017), p. 177-184
ISSN: 1612-3433 , , , :
Additive Fertigung durch selektives Elektronenstrahlschmelzen
In: Schweissen und Schneiden (2017), p. 30-39
ISSN: 0036-7184 , , , :
A multi-component evaporation model for beam melting processes
In: Modelling and Simulation in Materials Science and Engineering 25 (2017), Article No.: 025003
ISSN: 1361-651X
DOI: 10.1088/1361-651X/aa5289 , , :
A coupled Cellular Automaton–Lattice Boltzmann model for grain structure simulation during additive manufacturing
In: Computational Materials Science 124 (2016), p. 37-48
ISSN: 0927-0256
DOI: 10.1016/j.commatsci.2016.07.005 , , :
Multiscale Modeling of Powder Bed-Based Additive Manufacturing
In: Annual Review of Materials Research 46 (2016), p. 93-123
ISSN: 1531-7331
DOI: 10.1146/annurev-matsci-070115-032158 , :
Lattice Boltzmann method for Oldroyd-B fluids
In: Computers & Fluids 124 (2016), p. 190-196
ISSN: 0045-7930
DOI: 10.1016/j.compfluid.2015.08.004 , :
Numerical investigations on hatching process strategies for powder-bed-based additive manufacturing using an electron beam
In: International Journal of Advanced Manufacturing Technology 78 (2015), p. 239-247
ISSN: 0268-3768
DOI: 10.1007/s00170-014-6594-9
URL: http://link.springer.com/article/10.1007/s00170-014-6594-9 , , , :
Free surface Neumann boundary condition for the advection-diffusion lattice Boltzmann method
In: Journal of Computational Physics 301 (2015), p. 230-246
ISSN: 0021-9991
DOI: 10.1016/j.jcp.2015.08.033 , :
Evaporation model for beam based additive manufacturing using free surface lattice Boltzmann methods
In: Journal of Physics D: Applied Physics 47 (2014), Article No.: 275303
ISSN: 0022-3727
DOI: 10.1088/0022-3727/47/27/275303 , , :
Modelling of electron beam absorption in complex geometries
In: Journal of Physics D-Applied Physics 47 (2014), Article No.: 065307
ISSN: 0022-3727
DOI: 10.1088/0022-3727/47/6/065307 , , :
Validation Experiments for LBM Simulations of Electron Beam Melting
In: International Journal of Modern Physics C (2014), p. 1-9
ISSN: 0129-1831
DOI: 10.1142/S0129183114410095
URL: http://arxiv.org/pdf/1402.2440.pdf , , , , :
Defect generation and propagation mechanism during additive manufacturing by selective beam melting
In: Journal of Materials Processing Technology 214 (2014), p. 2522-2528
ISSN: 0924-0136
DOI: 10.1016/j.jmatprotec.2014.05.002 , , :
Simulating fast electron beam melting with a parallel thermal free surface lattice Boltzmann method
In: Computers & Mathematics with Applications 67 (2014), p. 318-330
ISSN: 0898-1221
DOI: 10.1016/j.camwa.2013.10.001
URL: http://www.sciencedirect.com/science/article/pii/S0898122113005944 , , , , :
Electron beam absorption algorithms for electron beam melting processes simulated by a three-dimensional thermal free surface lattice Boltzmann method in a distributed and parallel environment
In: Procedia Computer Science 18 (2013), p. 2127-2136
ISSN: 1877-0509
DOI: 10.1016/j.procs.2013.05.383
URL: http://www.sciencedirect.com/science/article/pii/S1877050913005267 , , , , :
Fundamental consolidation mechanisms during selective beam melting of powders
In: Modelling and Simulation in Materials Science and Engineering 21 (2013), Article No.: 085011
ISSN: 0965-0393
DOI: 10.1088/0965-0393/21/8/085011 , , :
Periodic open-cell foams: Pressure drop measurements and modeling of an ideal tetrakaidecahedra packing
In: Chemical Engineering Science 66 (2011), p. 2758-2763
ISSN: 0009-2509
DOI: 10.1016/j.ces.2011.03.031 , , , , , , :
Mesoscopic simulation of selective beam melting processes
In: Journal of Materials Processing Technology 211 (2011), p. 978-987
ISSN: 0924-0136
DOI: 10.1016/j.jmatprotec.2010.12.016 , , :
Lattice Boltzmann model for thermal free surface flows with liquid-solid phase transition
In: International Journal of Heat and Fluid Flow 32 (2011), p. 156-163
ISSN: 0142-727X
DOI: 10.1016/j.ijheatfluidflow.2010.09.006 , :
Lattice Boltzmann method for dynamic wetting problems
In: Journal of Colloid and Interface Science 335 (2009), p. 84-93
ISSN: 0021-9797
DOI: 10.1016/j.jcis.2009.02.055 , :
Optimization and Stabilization of LBM Free Surface FlowSimulations using Adaptive Parameterization
In: Computers & Fluids 35 (2006), p. 934-939
ISSN: 0045-7930
URL: http://www.sciencedirect.com/science/article/pii/S004579300500157X/pdfft?md5=59701b54104d0daae6791fd1b2140ffa&pid=1-s2.0-S004579300500157X-main.pdf , , , , :
Lattice Boltzmann Model for Free Surface Flow for Modeling Foaming
In: Journal of Statistical Physics 121 (2005), p. 179-196
ISSN: 0022-4715
DOI: 10.1007/s10955-005-8879-8
URL: http://citeseerx.ist.psu.edu/viewdoc/download?doi=10.1.1.321.499&rep=rep1&type=pdf , , , , :
Modeling of metal foaming with lattice Boltzmann automata
In: Advanced Engineering Materials 4 (2002), p. 765-769
ISSN: 1438-1656
DOI: 10.1002/1527-2648(20021014)4:103.0.CO;2-M , , :
Book Contributions
Parallel Lattice Boltzmann Methods for CFD Applications
In: Numerical Solution of Partial Differential Equations on Parallel Computers, New York: Springer, 2005, p. 439-465 (Lecture Notes in Computational Science and Engineering, Vol.51)
ISBN: 3-540-29076-1
URL: https://www10.informatik.uni-erlangen.de/Publications/Papers/2005/LBMCFD_LNCSE51.pdf , , , , :
The Physics of Foaming: Structure Formation and Stability
In: B. Kriszt, H. P. Degischer (ed.): Handbook of Cellular Metals, München: Wiley-VCH, 2002, p. 33-43
ISBN: 3-527-30339-1 , :
Conference Contributions
Accelerating Alloy Development for Additive Manufacturing
15th International Symposium on Superalloys, ISS 2024 (Pennsylvania, PA, 8. September 2024 - 12. September 2024)
In: Jonathan Cormier, Ian Edmonds, Stephane Forsik, Paraskevas Kontis, Corey O’Connell, Timothy Smith, Akane Suzuki, Sammy Tin, Jian Zhang (ed.): Minerals, Metals and Materials Series 2024
DOI: 10.1007/978-3-031-63937-1_11 , , , , , , :
SAMPLE3D: A versatile numerical tool for investigating texture and grain structure of materials processed by PBF processes
IVth International Conference on Simulation for Additive Manufacturing (Sim-AM 2023) (München, 26. July 2023 - 28. July 2023)
DOI: 10.23967/c.simam.2023.006 , , , , :
3D grain growth simulation and experimental verification in laser beam melting of IN718
10th CIRP Conference on Photonic Technologies (LANE 2018) (Fürth, 4. September 2018 - 6. September 2018)
In: Procedia CIRP 74 (2018) 2018
DOI: 10.1016/j.procir.2018.08.034
URL: https://www.sciencedirect.com/science/article/pii/S2212827118308187/pdf?md5=ea85f15a94f75d82fce787e5b0a20225πd=1-s2.0-S2212827118308187-main.pdf , , , , , :
Topology Optimization in Additive Manufacturing Considering the Grain Structure of Inconel 718 using Numerical Homogenization
iCAT 2018 (Maribor, 10. October 2018 - 11. October 2018)
In: Proceedings of 7th International Conference on Additive Technologies 2018 , , , , , , , , , :
3D multilayer grain structure simulation for beam-based additive manufacturing
2017 Simulation for Additive Manufacturing, Sinam 2017 (Munich, DEU, 11. October 2017 - 13. October 2017)
In: Simulation for Additive Manufacturing 2017, Sinam 2017 2017 , , :
Predictive numerical simulations of processing windows for powder bed based additive manufacturing
2017 Simulation for Additive Manufacturing, Sinam 2017 (Munich, 11. October 2017 - 13. October 2017)
In: Simulation for Additive Manufacturing 2017, Sinam 2017 2017 , , , , :
3D Grain Structure Simulation for Beam-Based Additive Manufacturing
6th International Conference on Additive Technologies iCAT (Nürnberg, 29. November 2017 - 30. November 2016)
In: Proceedings of the 6th International Conference on Additive Technologies iCAT 2016 2016 , , , :
Numerical Investigations of Selective Electron Beam Melting on the Powder Scale
Fraunhofer Direct Digital Manufacturing Conference 2016 (Berlin, 16. March 2016 - 17. March 2016)
In: Proceedings of the Fraunhofer Direct Digital Manufacturing Conference 2016 2016 , , , :
A Python extension for the massively parallel framework waLBerla
4th Workshop on Python for High Performance and Scientific Computing (New Orleans, 17. November 2014 - 17. November 2014)
In: online 2014
URL: http://www.dlr.de/sc/Portaldata/15/Resources/dokumente/pyhpc2014/submissions/pyhpc2014_submission_5.pdf , , , , , , :
Observation and numerical simulation of melt pool dynamic and beam powder interaction during selective electron beam melting
23rd Annual International Solid Freeform Fabrication Symposium - An Additive Manufacturing Conference, SFF 2012 (Austin, TX)
URL: https://www.scopus.com/inward/record.uri?partnerID=HzOxMe3b&scp=84889688177&origin=inward , , , :
Numerical Simulation of Foam Solidification Phenomena
MetFoam 2009 (Bratislava)
In: MetFoam 2009 - Proceedings of the 6th Interational Conference on Porous Matals and Metallic Foams 2009 , :
FreeWIHR: Lattice Boltzmann Methods with Free Surfaces and their Application in Material Technology
KONWIHR Results Workshop (Garching)
In: High Performance Computing in Science and Engineering, Garching 2004, Berlin/Heidelberg: 2005 , , , , :
Simulation of Metal Foam Formation with the Lattice Boltzmann Method
International Symposium on Cellular Metals and Polymers (Fürth)
In: R.F. Singer, C. Körner, V. Altstädt, H. Münstedt (ed.): Cellular Metals and Polymers, Zürich: 2005 , , , , :
Modelling of metal foaming by in-situ gas formation.
MetFoam 2001 (Bremen, 18. June 2001 - 20. June 2001)
In: J. Banhart, M. F. Ashby, N. A. Fleck (ed.): Cellular Metals and Foaming Technology, Bremen: 2001 , , , :
Experimental and Numerical Investigation of the Formation of Metal Foam
Materials Week 2000 (München, 25. September 2000 - 28. September 2000) , , , :
Numerical Simulation of Foam Formation and Evolution with Modified Cellular Automata
MetFoam '99 (Bremen)
In: J. Banhart, M. F. Ashby, N. A. Fleck (ed.): Metal Foams and Porous Metal Structures, Bremen: 1999 , :
Thesis
Modeling and Simulation of Bulk Metallic Glass Crystallization During Laser Powder Bed Fusion (Dissertation, 2024)
DOI: 10.25593/open-fau-715 :
Numerische Entwicklung von Superlegierungen für den Guss und die Additive Fertigung (Dissertation, 2024) :
Modeling of Selective Laser Sintering of Viscoelastic Polymers (Dissertation, 2019) :
Mesoskopische Simulation des selektiven Strahlschmelzens mittels einer Lattice Boltzmann Methode mit dynamischer Gitteranpassung (Dissertation, 2018) :
Simulation von Verdampfungsphänomenen beim selektiven Elektronenstrahlshmelzen (Dissertation, 2017) :
Numerische Modellierung und Simulation des selektiven Elektronenstrahlschmelzens basierend auf einer gekoppelten Gitter Boltzmann und Diskrete Element Methode (Dissertation, 2015) :
Simulation of Selective Electron Beam Melting Process (Dissertation, 2011) :
Modellierung des Schaumbildungsprozesses von Metallen mit Hilfe der Lattice-Boltzmann-Methode (Dissertation, 2005) :
Miscellaneous
Interactive Free Surface Fluids with the Lattice Boltzmann Method
(2005), p. 10
URL: https://www10.cs.fau.de/publications/reports/TechRep_2005-04.pdf , , :
FreeWiHR --- LBM with Free Surfaces
(2004), p. 15
URL: https://www10.cs.fau.de/publications/reports/TechRep_2004-06.pdf , , , , :
Simulation von Metallschaum mittels der Lattice-Boltzmann Methode
35 (2003), p. 4-8 , , , :
Funding source: DFG / Sonderforschungsbereich / Transregio (SFB / TRR)
Project leader:
A new numerical tool will be explored that supports the experimental alloy developer in defining new compositions with potential for high strength. Starting with a composition space that is defined by the developer based on his metallurgical experience and his design goals, the numerical tool will propose the most promising compositions. The research program will on the one hand address open questions regarding the mathematical optimization in this application and on the other hand new models for predicting the relevant material properties.
Funding source: Bundesministerium für Wirtschaft und Technologie (BMWi)
Project leader:
Funding source: DFG / Sonderforschungsbereich (SFB)
Project leader: ,
The aim of this project is to facilitate additive manufacturing of bulk metallic components by selective laser melting based on predictive numerical simulations. There should be developed suitable process strategies to ensure the amorphous material state preferably without aging effects in the bulk as well as for complex geometries. Therefore, clear statements using the numerical simulation has to be made exceeding the temperature field and the material consolidation during manufacturing towards the solidification behavior, aging and finally crystallization.
Funding source: DFG-Einzelförderung / Sachbeihilfe (EIN-SBH)
Project leader:
Funding source: DFG-Einzelförderung / Sachbeihilfe (EIN-SBH)
Project leader:
Beam-based additive manufacturing (AM) of metals in a powder bed not only offers the opportunity to build complex, custom-made components of high-performance materials, but also to adjust the local material properties by proficient processing. The variation of solidification conditions enables the modification of microstructure length scales. Additionally, latest research results indicate, that also the texture of the components is adjustable during manufacturing. Therefore, entirely new perspectives are opened regarding optimization of light weight components, because not only the topology, but also the texture of the material is adjustable to the local loads on the component. In order to comprehend and control the texture evolution, the hydrodynamic non-equilibrium solidification process (grain growth, selection and nucleation) needs to be fundamentally understood. Experimental investigations show that especially the mechanisms of nucleation under the extreme conditions of AM are insufficiently resolved and are not reproduced by classical models.The aim of this proposal is to identify, to fundamentally understand and to physically model the microstructure evolution, especially the nucleation under the special solidification. This model should be implemented in existing software, which is developed at our chair. Modeling and verification are experimentally substantiated basing on additively manufactured samples of IN718. At the end of the project the model should predict the solidification structure, grain structure and texture evolution during beam and powder bed-based AM.The project draws on our software for simulating the consolidation process during beam and powder bed-based AM. The software contains a lattice Boltzmann method to describe the hydro- and thermodynamics during melting and solidification. This method s coupled to a cellular automaton modeling the grain structure evolution during solidification neglecting currently grain nucleation. Our new theoretical ansatz contains besides the temperature gradient and the solidification front velocity for the first time additional information about the texture of the previous layers (orientation, spacing of cells/dendrites, segregation) and the local composition of the melt at the interface to the currently processed layer. It should be investigated, how orientation changes at the solidification front in combination with the present segregations in the rapidly melted material (memory of melt) induce grain nucleation by local undercooling. These findings are mathematically utilized for a grain nucleation model.
Funding source: DFG / Sonderforschungsbereich (SFB)
Project leader:
The basic mechanisms that are essential in the powder based selective beam melting process are poorly understood. Most of the existing analytical and numerical models describing the process of consolidation in a homogenized image, i.e. individual powder particles are not resolved. This approach is suitable for information on averages, but cannot capture the local influence of the powder, i.e. the powder size distribution, the stochastic effect of the powder bed, the wetting of the powder by the melt and the formation of the melt. The actual selective melting process and thereby acting mechanisms can only be understood on the scale of the powder particles, with the help of numerical simulation on the mesoscopic scale. The aim of this project is to provide a numerical tool for mesoscopic simulation of selective beam melting and to use it to develop innovative process strategies. The mesoscopic scale allows the prediction of defects, surface quality and accuracy of the structure for different materials as a function of material parameters (powder form, bulk density, ...) and the process parameters (beam shape, energy per unit length, speed, ...).
In the first phase, a tool for the 2D simulation of selective electron beam melting was developed and validated with experimental results. The main task was the modeling of the entire build process with its different time scales (pre-heating, melting, applying new powder layer). Among other things, the complex coupling of the beam in the powder bed, radiation losses at the surface, mass and energy loss through evaporation and the deformation of the molten bath by the evaporation pressure is taken into account. The software is now able to simulate assembly processes, taking into account different scanning strategies on many layers. Such process strategies as the remelt strategy and the refill strategy are investigated. The verification of the numerical results is done in close cooperation with subproject B2.
In the second phase, the previous model is transferred to polymers. For this purpose, the absorption of the laser beam in the partially transparent stochastic powder bed and the highly viscous, viscoelastic material behavior must be described. Development and verification of the model is carried out in cooperation with subproject B3. In a further step, a method of 3D simulation of the grain structure in the selective beam melting of metals is implemented, in order to predict the texture of the materials as a function of process strategy.
Funding source: EU - 7. RP / Cooperation / Verbundprojekt (CP)
Project leader:
The overarching goal of AMAZE is to rapidly produce large defect-free additively-manufactured (AM) metallic components up to 2 metres in size, ideally with close to zero waste, for use in the following high-tech sectors namely: aeronautics, space, automotive, nuclear fusion and tooling.
Four pilot-scale industrial AM factories will be established and enhanced, thereby giving EU manufacturers and end-users a world-dominant position with respect to AM production of high-value metallic parts, by 2016. A further aim is to achieve 50% cost reduction for finished parts, compared to traditional processing.
The project will design, demonstrate and deliver a modular streamlined work-flow at factory level, offering maximum processing flexibility during AM, a major reduction in non-added-value delays, as well as a 50% reduction in shop-floor space compared with conventional factories.
AMAZE will dramatically increase the commercial use of adaptronics, in-situ sensing, process feedback, novel post-processing and clean-rooms in AM, so that (i) overall quality levels are improved, (ii) dimensional accuracy is increased by 25% (iii) build rates are increased by a factor of 10, and (iv) industrial scrap rates are slashed to <5%. Scientifically, the critical links between alloy composition, powder/wire production, additive processing, microstructural evolution, defect formation and the final properties of metallic AM parts will be examined and understood. This knowledge will be used to validate multi-level process models that can predict AM processes, part quality and performance. In order to turn additive manufacturing into a mainstream industrial process, a sharp focus will also be drawn on pre-normative work, standardisation and certification, in collaboration with ISO, ASTM and ECSS. The team comprises 31 partners: 21 from industry, 8 from academia and 2 from intergovernmental agencies. This represent the largest and most ambitious team ever assembled on this topic.
Funding source: Sonstige EU-Programme (z. B. RFCS, DG Health, IMI, Artemis)
Project leader:
Funding source: EU - 7. RP / Capacities / Forschung für spezielle Gruppen (insbesondere KMU) (SME)
Project leader:
Electron beam melting additive manufacturing is used to produce successive layers of a part in a powder bed and offers the ability to produce components closest to their final dimensions, with good surface finish. At this time the process is faster than any other technique of comparable quality, however the parts are not produced at sufficient rate to make them economically viable for any but very high value specific applications. One key output of the project will be the knowledge surrounding the use of the high powder electron beam gun, including the process control, and modeled and validated understanding of beam-powder bed interaction. The target objectives is the transfer of the 2D model to a 3D model and its parallel implementation. The outcome of the simulation will be compared with real experimental data and therefore the model parameters are adjusted in such a way that the resulting numerical melt pool sizes correspond to the experimental ones.
Funding source: DFG-Einzelförderung / Sachbeihilfe (EIN-SBH)
Project leader:
Geschäumte Materialien stellen aufgrund ihrer zellularen Struktur eine interessante Materialklasse mit attraktiven Eigenschaften dar. Unabhängig vom Material ist die Schaumbildung im Allgemeinen wenig verstanden und die Schaumherstellung basiert im Wesentlichen auf dem Trial-and-Error-Prinzip. Die numerische Simulation eröffnet hier neue Wege, grundlegende Phänomene bei der Schaumbildung zu er-forschen und die daraus abgeleiteten Erkenntnisse praktisch umzusetzen. Basis für das beantragte Proj…
Funding source: DFG-Einzelförderung / Sachbeihilfe (EIN-SBH)
Project leader:
Project leader: ,
In the last few years methods, cellular automata (CA) became increasingly popular to simulate the physical phenomena that have to be considered when developing and manufacturing new materials. Among these phenomena are the formation of grain structures or dendrites during solidification. A special CA called Lattice Gas or Lattice Boltzmann Method (LBM) is perfectly suited for modeling flows in complex and time- dependent geometries as they are encountered in the context of metal foams or of composite…
Project leader:
A predictive software relies on exact physical and numerical models. The most important aspect is the correct modelling of the thermal conditions. Almost all modifications of process parameters have a direct influence on heat conduction, the coupling of the energy source or heat sinks by e.g. heat radiation or evaporation. Furthermore, many material parameters are temperature dependent and sensitive to a correct model. During melting a melt pool evolves, whose dynamics are mainly covered by capillarity, wetting, Marangoni convection and gravity. The temperature gradient and the solidification velocity mainly influence the final microstructure while solidification.
Project leader:
The 2D simulation software SAMPLE2D of selective electron beam melting bases on the software for modelling of foam formation. The base software is extended by certain modules comprising the electron beam absorption, phase transitions, (selective evaporation or grain structure evolution. After a careful experimental validation, the aim of this software is to predict process windows and explain process phenomena.
Project leader:
Most process phenomena during selective electron beam melting are covered by a 2D simulation. A more realistic modelling of the melt pool dynamics and the grain structure evolution is reached by 3D simulations. Therefore, two different simulation tools for these purposes are developed at WTM.
The 3D hydrodynamics software SAMPLE3D requires a massively parallel implementation, which has been developed in cooperation with the chair of system simulation. The melt pool dynamics and the material consolidation are investigated in full spatial dimension. Using this software, process windows for dense parts as well as innovative process strategy modifications are predicted.
The grain structure evolution is modeled by the separate software SAMPLE3DGS, which enables the grains to grow in all possible directions during processing. Here, a macroscopic approach is used, where the powder particles are approximated by a continuum. Additionally, only the thermodynamics are modelled. With these simplifications, domains on the scale of whole parts are possible to simulate.
Project leader:
To study the selective laser melting of polymers, the current numerical model for metals is transferred for viscoelastic materials. Therefore, the energy coupling of the laser source is modified regarding the different absorption and reflexion behavior of photons on polymers, e.g., the material is semi-transparent in its liquid state. Additionally, the rheological model for highly viscous and viscoelastic materials from the foam formation is reused.
Project leader:
In this group a numerical tool for multi-criteria optimization is developed. In particular, it is applied on the alloy development of nickel-based superalloys. The scientific research focuses on probabilistic and deterministic models to find all optimum solutions (pareto front) in the search space. By the development of the CALPHAD method in the recent decades, new opportunities to extend the classical alloy development by means of the prediction of physical properties and microstructure arose. Most property models base on thermodynamic and kinetic calculations, which are coupled by the TC API to the commercial software ThermoCalc and DICTRA.
The research is funded by the collaborative research center SFB Transregio 103 (http://www.sfb-transregio103.de/).
Project leader:
Until today, metallic foams are not common despite their potential for energy absorption and ultra-light components. The main disadvantage are the inhomogenities of the pore structure, which includes variations in the pore size, geometry and wall size. The aim is to understand the underlying effects during foam formation to improve the process.
The implemented software bases on the lattice Boltzmann method, covers he most important physical effects during foam formation and is able to predict modified process strategies. The implementation comprises the hydrodynamic, diffusive and thermodynamic conservation equations applied on free surfaces. The physical models cover the growth, coarsening, reordering and collapse of foam bubbles as well as effects of the whole pore network like aging and drainage due to capillarity and wetting.
Project leader:
Foam materials are due to their cellular structure an interesting material class with attractive properties. The software used for metal foams was extended to simulate the viscoelastic effects during foaming of polymers. Therefore, the numerical method was extended by a rheological model for viscoelastic fluids applied on free surfaces. With this software, the influence of different process parameters on the foam formation was studied.
Funding source: DFG - Sonderforschungsbereiche
Project leader: ,
Based on the gained knowledge of projects B4 and C5, the aim of this project is to account for the influence of part borders on the resulting material/part-mesostructure for powder- and beam-based additive manufacturing technologies of metals and to model the resulting meso- and macroscopic mechanical properties. The mechanical behavior of these mesostructures and the influence of the inevitable process-based geometrical uncertainties is modelled, verified, quantified and validated especially for cellular grid-based structures.